Rethinking CO2 capture and storage
2022/03/24
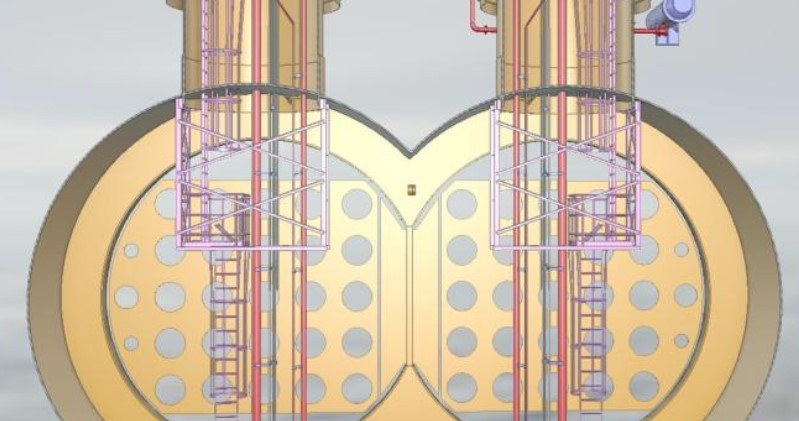
Bi nut
How tank design and cargo handling systems can support environmental goals
Amid global urgency to reduce carbon emissions, Carbon Capture and Storage (CCS) technology is developing at pace. CCS works by capturing carbon from its sources at industrial sites and processing it into liquified CO2. The CO2 in liquid form is then transported to a shore-based terminal, from where it is carried in pipes to underground storage locations. Very soon, the maritime transportation element will be a vital part of the CCS chain, adding new technologies to increase the carrying capacity of captured CO2 in a commercially viable way. At Høglund, we are using our engineering knowledge and systems expertise to bring these technologies to the market.
The case of liquified CO2 transportation
Demand for the maritime transportation of liquified CO2 – already used in the food and drink industry - is set to increase drastically as global CCS chains develop in response to the pressing need to reduce industrial emissions. To respond to this demand, the maximum carrying capacity for ship-borne CO2 transportation must increase drastically – which brings along some unique challenges for tank design and cargo handling.
Currently, the maximum capacity for transporting liquified CO2 by ship is 3,600cbm, or 1,700 tonnes in dedicated CO2 tankers. Liquid CO2 is stored and transported at -35 degrees C at a high pressure of 15 bar, alongside a safety margin. This extra accommodation for safety means that tanks intended for transporting liquid CO2 must be significantly thicker than other available tanks. This balance between capacity, tank thickness and size adds a layer of complexity when developing the CO2 transportation solutions that could significantly up-scale existing capacity.
The challenges – a combination of pressure, tanker characteristics and safety concerns
Escalating the size of tank design presents a notable challenge, because the thickness of the tank needed for the high pressures of the liquid CO2 increases the weight and size of the tank. Expanding the typical mono-lobe tanks for this size and capacity also means vessels need to carry more ballast water in order to mitigate stability issues, increasing once again the complexity of design required.
Additionally, many safety concerns surround the transportation of CO2. One of these comes from the management of the cargo itself. Pressure differences that arise from cargo handling as a result of a leak or fault in the cargo handling system could result in the sublimation of the CO2 to form blocks of dry ice that occlude safety relief valves. If unchecked, the whole tank could turn to dry ice.
The alternatives – redefining tank design and cargo handling systems
If escalating the size of tank presents challenges, what are the alternatives to scaling up existing mono-lobe designs?
Throughout the last couple of years, our teams of automation, gas, and hybrid systems engineers and designers at Høglund have collaborated with marine and tank design engineers from our partner company HB Hunte. Together, we have combined our expertise to develop gas and onboard cargo handling systems, integrated in Høglund’s automation and control system, that would be needed for an 8,000cbm bi-lobe type C CO2 storage tank.
This bi-lobe design increases cargo capacity by more than doubling the existing maximum one - currently set at 3,600cbm – and exceeding what could be achieved by scaling up a mono-lobe design. Additionally, this bi-lobe shaped tank comes without the size, accommodation, weight, and stability concerns that would come from scaling up the mono-lobe concept. At only 37 metres long and 2.4 metres in diameter, the bi-lobe design in fact assists in supporting vessel stability, in complete opposition to the added complexities that would arise from a mono-lobe tank of similar size and weight.
The bi-lobe tank shape has already been manufactured in Asia and Europe and used on sailing LPG, LEG and LNG tankers. The design is IGC code-compliant and made from steel alloys P690, VLF550 or A645. Given that the design can be manufactured with existing fabrication processes, the production of the tanks can be relatively cheap and quick, minimising any potential commercial risks arising with this new solution.
Cargo handling systems – championing safety and sustainability
For any marine technology and transportation hardware for tankers, safety is paramount. This is why the design of the new tank and the associated cargo handling, automation and integration systems have been developed to ensure this.
Høglund’s cargo handling system (CHS) prevents dry-ice formation and allows the CO2 to discharge even in the unlikely event the tank’s two deep-well pumps fail. The tanks are also insulated with 200mm of sprayed polyurethane to maintain the -35oC needed for liquified CO2. For added safety and operational support, vessel owners can monitor the system remotely in real-time.
The bi-lobe tank solution can be integrated into existing tanker designs. However, as shipping pushes towards a more sustainable future, we have been working with our project partners at Larvik Shipping - experts in CO2 transportation - for a new efficient tanker vessel design anchored around this new solution. Our collaboration has successfully delivered the creation of an ambitious 130m long and 9m wide LNG-fuelled tanker design.
At Høglund we believe that industry collaboration and partnerships is the approach that the shipping industry needs to take to move forward. The solutions we have developed in the CCS space are a result of extensive collaboration amongst various project partners, where we always aim to drawing on the relevant expertise of each. By also looking to expand and build upon existing, proven technologies, we have worked together for a solution that not only supports existing markets, but also represents a significant asset for the emerging CCS chain sector in a minimally disruptive way.
We are guided by this mindset to continue to lead the shipping industry on its technological transformation journey, as it aspires towards a more sustainable position in the global economy. Partnerships and collaboration will enable this transformation to happen at the pace and scale that is needed.