How the tech to decarbonize shipping already exists, part 1: Hydrogen
2022/04/25
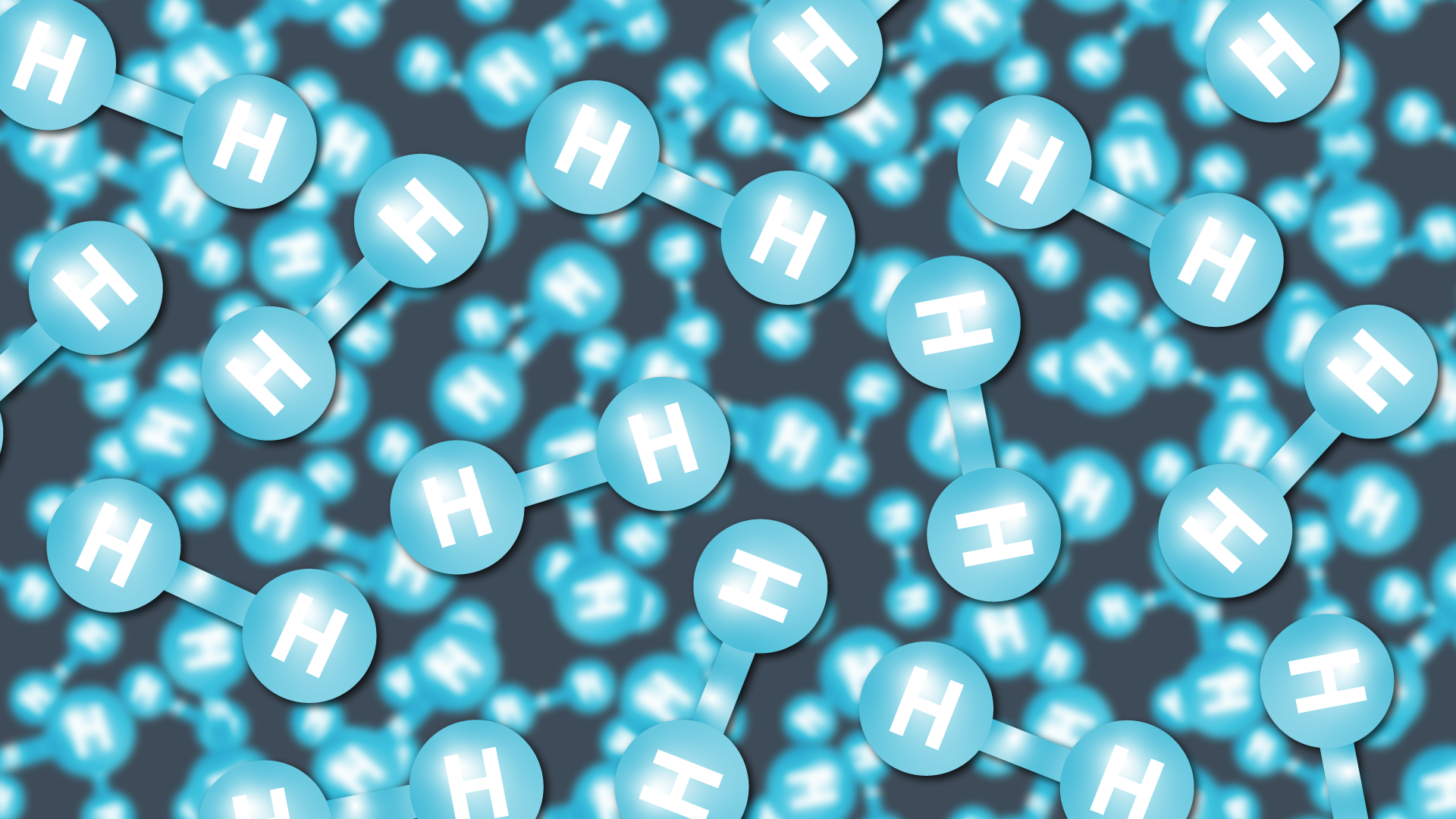
Hydrogen illustration
As alternative fuels enter the market, and pressure grows on owners to decarbonise, one of the highest strategic priorities is to ensure that a fleet can keep its options open and remain future proof.
Speaking at Nor-Shipping this year, for example, shipowners were told that the ability to secure ESG investment (investment tied to environmental, social and governance) goals is no longer a nice-to-have way of diversifying a portfolio – but a “condition to keep your investors,” according to Stephane Boujnah, chief executive of stock exchange group Euronext[1].
The challenge for owners is that prices and availability of low and zero carbon fuels remain uncertain. Building the infrastructure for a fully decarbonised marine fuel supply chain will take time, and in the time being, zero or low carbon fuels will be geographically limited, and expensive[2]. Shipping companies must therefore rely on existing technology to do what they can with the alternative fuels that are on the table right now – such as green hydrogen, green ammonia, bio and synthetic methanol, and bio and synthetic methane (also known as LNG) – to cut emissions.
But which of those fuels is the best, most effective energy source for steering maritime towards a zero-carbon future? In our first of three blogs on alternative fuels and decarbonisation technology, we explore the options on the table for owners, and what it means from a systems integration perspective.
Green hydrogen
This is made from a chemical process known as electrolysis: the splitting of hydrogen from oxygen in water using an electrical current. If the electricity used is obtained from renewable sources such as wind, solar or wave power, the end-product, hydrogen, will therefore be green and zero-carbon.
When considering the merits of green hydrogen as an energy carrier on board ships, one of the major pain points is that even in liquid form, hydrogen has a very low volumetric energy density. This means a huge quantity is required to produce sufficient energy. Additionally, to maximise this low-energy density, green hydrogen needs to be liquefied by storing it at around -250 Celsius – which is no easy feat.
While these issues aren’t the only challenges to using green hydrogen as a marine fuel, they are the biggest technological barriers. Hydrogen is extremely flammable when it mixes with oxygen, an oxidising agent, and is susceptible to leakages, making it problematic from a fuel-handling perspective. However, this is easily remedied through established design solutions and approaches to mitigate risks, such as spark-proof electrical equipment and safe storage rooms in hazardous areas.
Loading and storing hydrogen is achievable, as we saw with the recently launched Japanese Suiso Frontier tanker ship – a pilot project to transport brown hydrogen produced from coal on the world’s first liquefied hydrogen tanker. Moreover, vessels that use fuel cell technology to run on green hydrogen are being developed.
Elsewhere, some companies have created product roadmaps for launching conventional internal combustion engines that can be powered by new fuels. While the schedule for rolling out these engines is unclear, it’s expected they will be fuelled 100% by hydrogen.
What does this mean for marine systems?
It will be important for systems integrators and energy systems experts to be involved from the outset in the design of hydrogen vessels and carriers. Successfully innovating this new segment requires a new level of systems expertise that is often overlooked in the design process. Automation and fuel handling systems must be integrated and must be prioritised accordingly.
By considering how energy can be transferred, stored, and used on board a vessel today and in the future, as well as identifying the similarities and compatibilities across different energy carriers, shipowners can equip their vessels with a multiple use dual-fuel (MDF) system.
A vessel equipped with a dual-fuel system on board where one fuel system is designed for handling a low vapour pressure combustible liquid at ambient pressures and temperatures, and the other to handle a cryogenic, pressurized combustible and toxic energy carrier - both feeding into an internal combustion engine - will most likely cover practically any option the future might bring.
When it comes to hydrogen, the extreme low temperatures involved present the biggest technical hurdles to overcome. LNG bunkering introduced similar challenges – and LNG bunker vessels benefitted from close integration between automation systems and fuel handling.
In the case of hydrogen, we can see how decarbonisation is requiring new thinking in the gas handling world, iterating on what has been done in the field of LNG. At Høglund, for example, we have worked on tank concepts for CO2 tankers, that take designs from the LNG field and, relying on careful systems integration, increase capacity. Hydrogen transport will require this same application of expertise.